TOP 自分の思い 邪馬台国 バイク 瓢箪 霊場巡り 囲碁と将棋 CAD/CAM 生産管理 海外の思い出 索引
所要量計算講座
4.変動発注点方式
先の発注点方式では需要の変化に追随するには
常時発注点を人間が見直さなければならなかった
部品点数が少ないなら可能かもしれないが多くなる
と大変である
そこで、先々の使用量を生産計画を使用して計算し、
該当する部品発注点を定期的に見直す作業を自動化
したらどうかというのが、この方式である
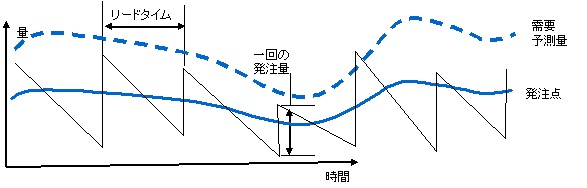
受注生産の場合、生産計画の様に厳密に作りずらい
ことがある
その場合、代表製品で需要予測を営業に作ってもらう
代表製品とするのは受注製品がその都度顧客要望で
使用する部品を変更したり、特注部品を使用したり、
製品名がその都度であったりすることがあるためである
部品の発注に使用するので、特殊な部品構成にする
のも一案である、例えばふたの色が5種類ある場合は
過去の販売例から比率を構成として登録する
つまり部品点数を整数でなく0.2や0.5といった風に
少数にして部品注文が販売数に比例して行われるような
工夫を入れる
あるいは製品をいくつかまとめて構成として持つような
親構成を持ち、その部品点数に販売比率を設定すると
いった工夫をするとよい
基本的に発注点なので在庫は常に存在するため、
急な受注や追加注文があっても少量ならば対応できる
運用の方法として部品単位で計画に対する実需の
変動率を発注点の何パーセントに設定するかを設定
できる
後に説明する世に名高いMRP方式では計画通りに
生産することが前提であり、また在庫はゼロになるよう
に計算するため、計画が不正確な受注生産には不向
きである
この変動発注点方式でも予測を超える需要の変動が
あった場合は対応不可能だが、本来想定外に対応
できる仕組みは理論的にあり得ないのであるから、
想定内に収まる受注生産に向いた考え方ではないかと
自負している
自負していると書いたのは、この方法は教科書には
載っていないからである
筆者は発注システムとして運用経験があるが、先に
述べた想定外(需要予測以上に売れた)で運用が破たん
するまで比較的好評であったことを報告しておく
長所:
在庫が少なくて済む
受注リードタイムが最終組み立てラインのリードタイム
で運用可能、つまり受注生産に対応可能
MRPよりも運用がルーズで良い
在庫の発注点比率を設定可能、この比率で計画と実需
の差異を設定できる
部品単位で設定するため面倒だが、逆に専用部品と共通
部品で比率を変えられる
筆者の場合、パターンをいくつか用意し、その番号で運用
担当に指定して貰う方式にした
またこの方式は需要予測さえ出来れば、サービスパーツ
にも応用可能である
サービスパーツのデッドストックに頭を悩ませている方は
応用を考えられたい
短所:
手作りのためシステム開発コストがかかる
理論は簡単なのだが経営陣には理解不可能のため承認
を得る手続きで若干揉める
・なぜパッケージ販売されているMRPではだめなのか
・単なる発注点とどう違うのか
・・・
所詮コストパフォーマンスとか実施時期しか眼中にないため
製造系でない経営者は理解しようとさえしない
在庫ありきのため、デッドストックも出るため、在庫量は計画
発注方式に及ばない
次は計画発注方式の一番手として製番方式を説明する
なお、後補充方式は別途説明済みなので省略する
またMRP方式も同様に省略
TOP 次へ